A house for 21 designs

The Japanese tradition of yakisugi involves burning—charring—wood to preserve it. Engineers Jon and Jesús Gasca had in mind the same idea that underpins the entire production of their company Stua : permanence over time. To achieve this, they needed a building that breathed nature, a headquarters for their firm—which has won the National Design Award —that respected the environment, and an up-to-date, mechanized factory capable of anticipating future needs.
When designing it, they used accoya wood— a radiata pine obtained from sustainable sources—which intertwines with a bamboo forest on the perimeter of the property. They also relied on Tinko Engineering , which signed the project with them under the direction of Jon Arratibel.
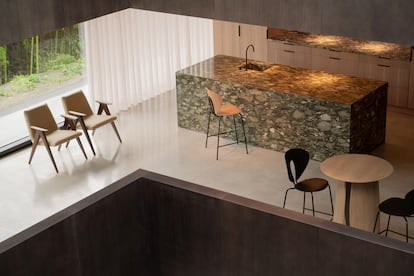
The bare, almost raw, open, and versatile interior design is by Jon Gasca and Javier Guerrero. It is, in fact, a framework for the 21 products sold by this San Sebastián-based company. It is also an echo of its versatility.
They only produce 21 products. At Stua, they don't produce furniture; they design and manufacture it. Father and son Jesús and Jon Gasca conceived the idea and manufactured it entirely there, in San Sebastián, since Jesús Gasca and Marina Quevedo founded the company in 1983. In forty years, they've only added 21 chairs, tables, and sofas to their catalog. All of these products remain for sale. What does that mean? They're all still relevant, competitive, and that's why they've found a niche in the market.
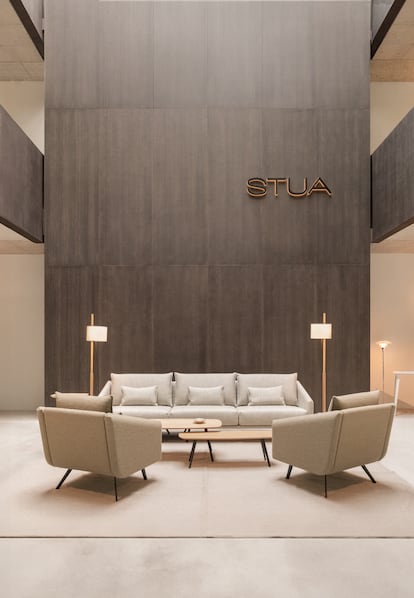
Stua doesn't introduce new things; it launches ideas onto the market. This isn't a company that sets or follows trends. That's why its products endure over time, because they don't arrive swept away by fads or trends; they arrive to offer solutions. This is precisely what its new headquarters demonstrates.
This company pays attention to every inch as much as every meter. This is evident, for example, in the plastic lining used to package its pieces—which has an elastic band, like a shower cap, allowing the plastic to be recycled as a cover for the furniture during moves or long absences. Something similar happens with the upholstery. In this factory, they don't staple, they just use a cord that gathers the leather around the seats and backrests.
The design of the sofas also allows for the accumulation of structures, optimizing warehouse and factory space. And the cutting of the wood is a logistical process that utilizes every scrap of material to manufacture a smaller piece. They are engineers. They master efficiency. That's why, when designing a building, they sought to convey those values.
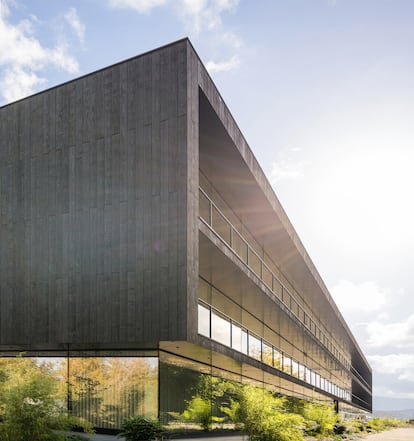
Thus, its three-story headquarters, nestled between a bamboo forest and a stream, serves as both a calling card and a summary of its ideology. It embodies a dialogue between nature and manufacturing. And it is, in itself, the sum of three connected volumes.
The automated warehouse—a 1,000-square-meter facility—is built with a metal structure and a sheet metal facade. More than a building, it's a mechanism. The same materials have been used for the factory, which occupies 4,000 square meters on the lower floor and another 3,000 square meters on the upper floor.
The centerpiece of the complex, the office building, is the smallest yet the most visible. With a façade of accoya wood, burned according to the yakisugi tradition, and a concrete structure, on three floors of 1,000 square meters—dedicated to residential, office, and contract spaces—it maintains a dialogue with the vegetation from each opening in the showroom and offices. A large central atrium differentiates these two services and bridges the gap between the bamboo and climbing plants of the exterior and the monstera plants of the interior.
The dialogue at the headquarters isn't just between the building and the location. As a flexible space, its walls represent the versatility of the designs, the 21 products they use to furnish homes, restaurants, museums, and entire offices. Without needing anything else. Creating ideas, away from trends.
EL PAÍS